Cut Quality Control Headaches and Improve Product Quality with Centric Final Inspection Module
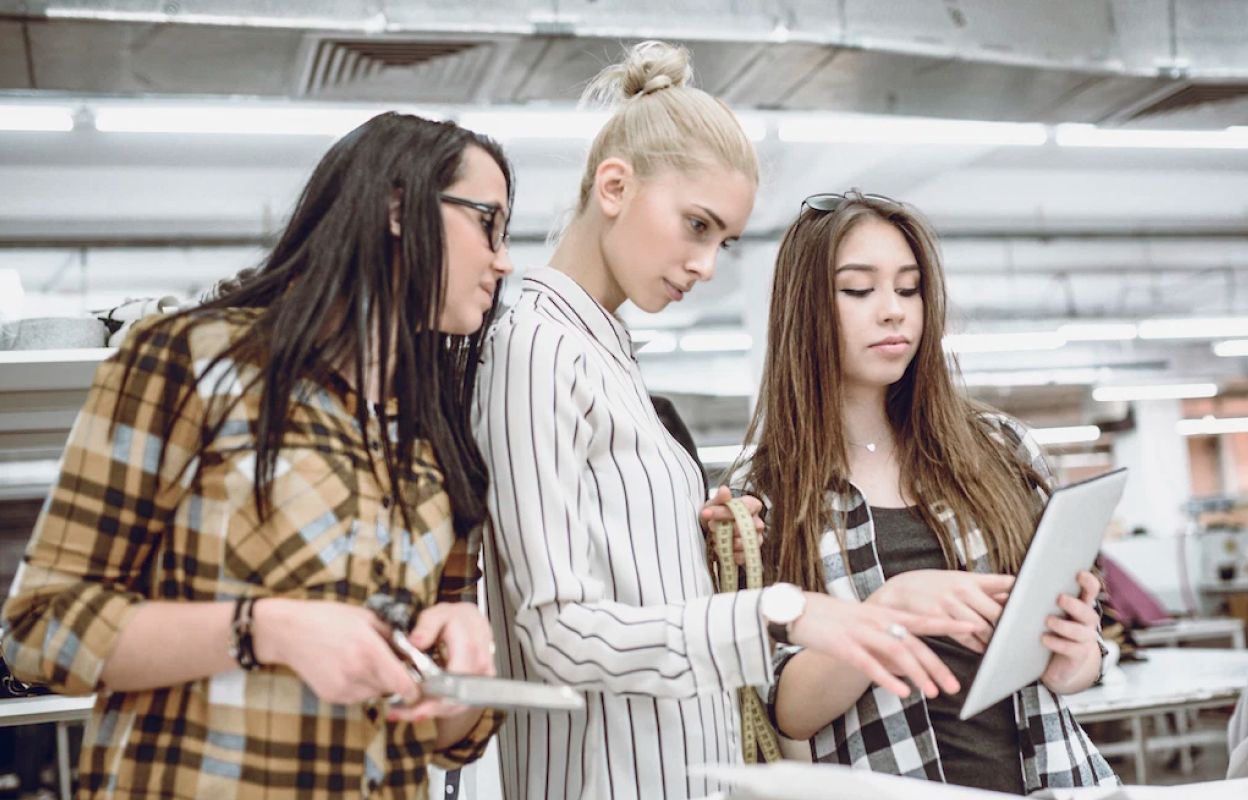
How Final Inspection Cuts Quality Control Headaches Without Cutting Corners
Ever been through the Acceptance Quality Limit (AQL) inspection process on the factory floor? It’s hot, noisy and busy. You’ve got a clipboard with a bunch of notes and a report template printed from a PDF. Some of the information might already be out of date. Some of the inspection points aren’t relevant to the product in question, but you had better fill in the whole report anyway.
You eventually get the opportunity to scan in your report, type up notes and send it off to the quality manager, who might be on the other side of the world…and that process has to be repeated for every product inspected.
There has to be a better way…right? Here’s how the Centric PLM Final Inspection module and mobile app blasts through the biggest barriers in quality control.
Streamlined Inspections, Faster Results
Final inspection, also known as AQL, is the last quality gate that ensures your products are made to spec and the workmanship is up to scratch in order to protect your brand reputation and ensure customer satisfaction. Whether it happens before products leave the factory or on arrival in the warehouse, and whether your business does its own quality checks or employs a third party, it is a critical step in the product lifecycle where cutting corners can have devastating consequences.
The problem is that it’s such a time-consuming process. Centric partners tell us it can take up to two hours to set up and schedule an inspection for just one product. When you have hundreds of products across multiple factories, the hours quickly add up.
Centric Final Inspection takes an entirely digital approach to save time and streamline the inspection process. Final Inspection exists as a module in Centric PLM and mobile app. Inspectors can use the mobile app on site to get a clear, real-time view of the products they need to inspect.
As inspectors enter information, notes and comments into the app, they see a real-time representation of the progress of the inspection. Quality managers can flag critical inspection points or customize report templates so that inspectors can cut through unnecessary information and complete inspections faster. When the inspection is finished, the inspector simply syncs the information with Centric PLM when an internet connection is available. The time lag between inspections and reports arriving is cut dramatically, making it easier to address quality issues quickly.
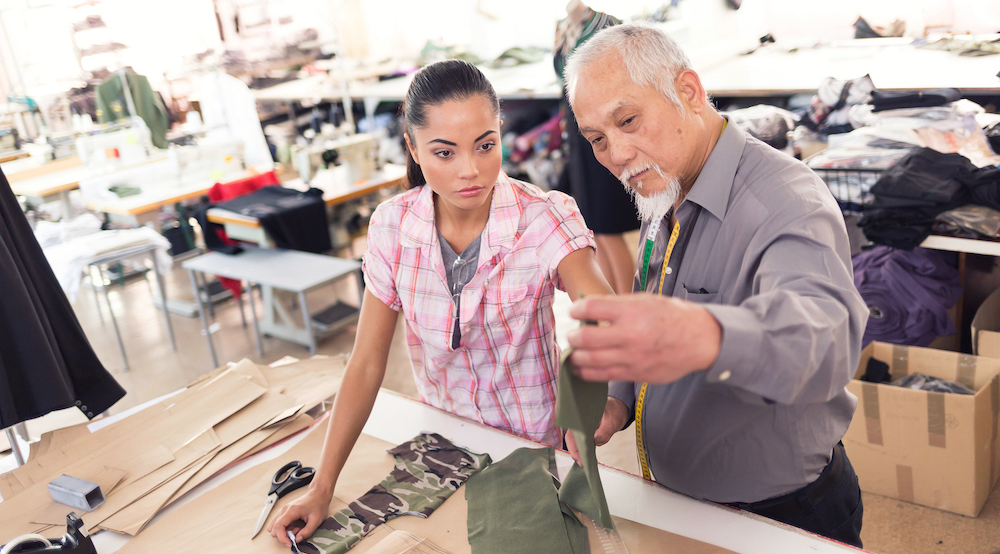
Always Up-to-Date Data
Of course, that means no more printed out PDFs. No more outdated or irrelevant report templates. No more handwritten notes in one place and photos in another place that have to be brought together and no more lugging everything around while traveling. Inspectors simply work in the desktop, web or mobile app all with online and offline capabilities, going through a list of inspection points and adding photos or comments along the way.
Because product information is pulled directly from Centric PLM, which offers a single source of the truth for data, it is much more likely to be up-to-date and relevant to inspectors. Centric PLM’s powerful AQL libraries capture and retain information on defects, inspection levels and tolerances that can be accessed via the module. Purchase order or shipment data from your system of records can be entered or interfaced with PLM, so that you have the relevant order and shipment quantities needed to derive the batch for inspection.
Analytics Drive Continuous Improvement
Centric has digitized the entire process with no data breakpoints from end to end. Because of that, it’s possible to analyze products, materials and supplier performance at a defect level to identify root causes for problems and support continuous product improvement. The Final Inspection module and mobile app help you confirm goods meet compliance standards prior to taking legal possession and financial responsibility for goods which means giving up any legal recourse if quality problems are found later-all which can lead to time consuming and costly headaches. Powerful analytics and reports allow you to slice and dice inspection information by product, style, defect type, supplier, factory and other characteristics to give you clear visibility.
By combining tech pack data with inspection templates, the Final Inspection module and mobile app automate the inspection process, vastly reduces inspection times and enables analysis for future decision-making. With Final Inspection, you can anticipate errors, collate detailed information for supplier reviews and address quality challenges that could undermine the success of your brand.
Why consider the Final Inspection and mobile app? If you want to cut the amount of time spent on product inspections without cutting corners, spot manufacturing issues quickly, analyze defect trends to avoid future mistakes and work more closely with vendors to improve products, going digital for your quality assurance process is a no-brainer.